Gold Haig Solutions

Horizontal high-energy magnetic grinding system
Unique advantages of horizontal high-energy magnetic grinding system:
1. High degree of automation, with a production capacity of ≥ 10 units per unit on this line;
2. With low investment and high return, it can meet the development needs of customers in the next 5-10 years;
3. Humanized design of the machine, equipped with automatic liquid adding function and automatic cooling and circulation function of the workbench, convenient exchange of containers and fixtures, suitable for various products;
4. Configuration can be selected according to customer needs, effectively reducing personnel intensity and improving machine productivity;
5. Standard configuration: manual replenishment;
6. Optional: Automatic material preparation and feeding system.
Project Case: Die-casting and other projects;
Applicable materials: aluminum alloy, zinc alloy, and other materials;
Application time: 2015 to present.
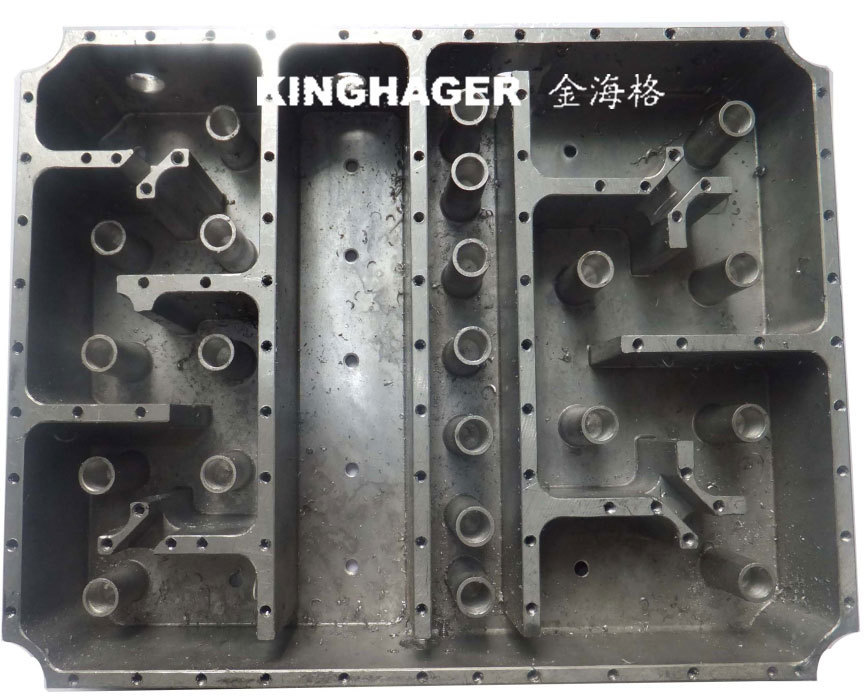
Before
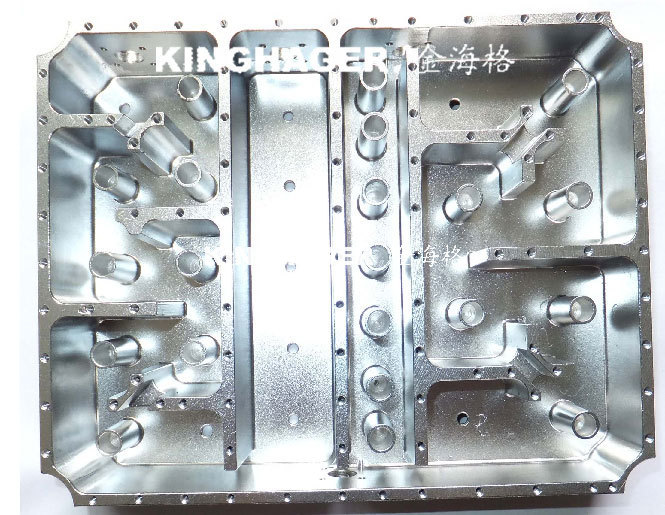
After

Automatic rolling and polishing equipment
Advantages of automatic rolling and polishing equipment:
1. It can achieve rapid batch automation operations;
2. Significantly reducing the intensity of human operations and;
3. Labor costs, achieving equipment automation and intelligence.
Project cases: aluminum alloy, Apple phone, computer case, and other projects;
Applicable materials: aluminum alloy, steel parts, and other materials;
Application time: Since 2016.
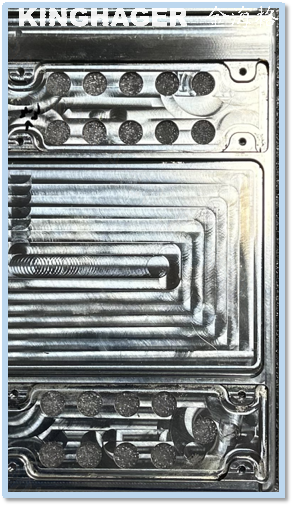
Before
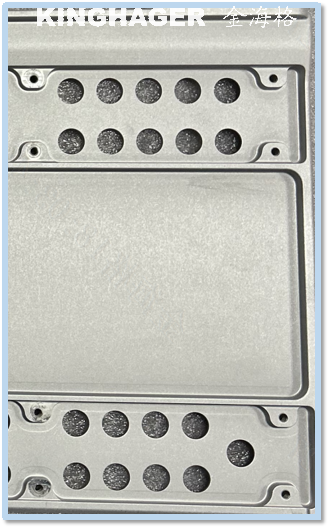
After

3D intelligent polishing machining center
Equipment advantages of 3D intelligent polishing five axis machine:
1. We can design 3/4/6 workstation models according to different customer product requirements;
2. Can cooperate with single machine automation connection projects or upgrade and renovation.
Project case: WHTCH watches, mirror products, and other projects;
Applicable materials: aluminum alloy, zinc alloy, and other materials;
Application time: Since 2019.
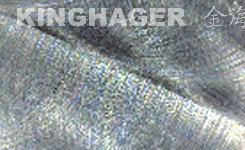
Before
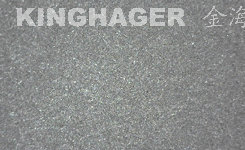
After

Automated Solution for High Energy Magnetic Surface Treatment
Equipment advantages of high-energy magnetic surface treatment automation solutions:
1. Humanized control panel and control system, with screen self-locking function;
2. The frequency of the magnetic field and the time of magnetic oscillation can be manually set;
3. It has the function of automatic memory, storage, and recall, deletion of set parameters;
4. Reminder for regular replacement of polishing fluid;
5. System automatic diagnosis of errors, abnormal operation, and alarm functions;
6. Automatic management function for grinding fluid lifespan - liquid change prompt function, with controllable grinding fluid lifespan; Improve the service life of grinding oil and reduce the cost of consumables;
7. Multiple processing modes: ordinary and mobile (with mobile function on/off), multifunctional grinding and polishing without dead corners, and all parts of the workpiece are completely polished and polished;
8. The equipment can achieve the best grinding and polishing effect and the highest grinding and polishing efficiency by cooperating with the original factory grinding materials and auxiliary materials
Project Case: National Fiber Optic Cable, Aerospace Parts and Other Projects;
Applicable materials: copper, copper alloy, and other materials;
Application time: 2022 to present.
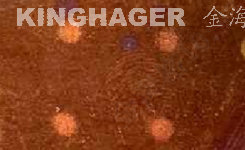
Before
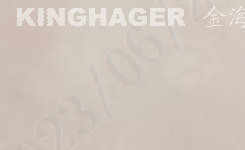
After

High energy magnetic automation system equipment
Advantages of high-energy magnetic automation system equipment:
1. Grinding → Pouring → Vibration spraying (product and abrasive separation) → Discharging;
2. Automatic recycling, circulation and filtration of grinding fluid;
3. PLC human-machine interface control, which can set and store multiple sets of grinding program parameters, has a high degree of automation and is convenient for workers to operate. A single person can operate multiple machines, with low work intensity;
4. Optional: Grinding needle automatic recovery+automatic material preparation and feeding system.
Project cases: AUTOLIV, TAKATA safety buckle, SR SUNTOUR pedal and other projects;
Applicable materials: zinc alloy, aluminum alloy, copper and other metal components;
Application time: 2012 to present.
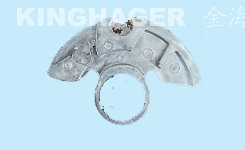
Before
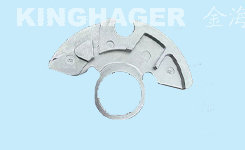
After

Fully automatic loading and unloading+grinding+cleaning and drying system
Advantages of fully automatic loading and unloading, grinding, cleaning and drying system equipment:
1. Design loading/unloading machine hands and workpiece transfer fixtures to automatically complete grinding cleaning drying cycle selection;
2. Intelligent control, voice operation step prompts, controllability of each link, selection of multiple material numbers, display of alarm positions, etc,
3. Intelligent control to achieve IoT connectivity of client MES systems.
Project case: Automotive steering system and other projects;
Applicable materials: aluminum alloy and other metal components;
Application time: Since 2016.
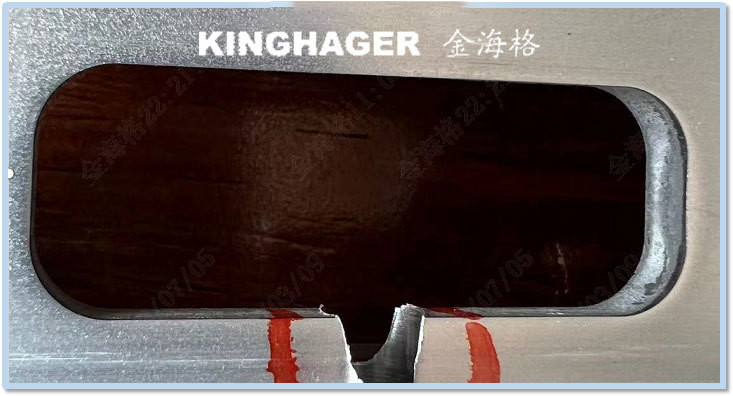
Before
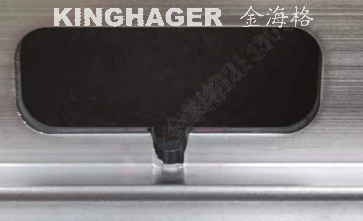
After

Wet fully automatic deburring system
Advantages of wet fully automatic deburring system:
1. Design and select a 6-axis robot to achieve fully automatic loading and unloading;
2. Wet grinding for deburring, with no dust generated during the process, achieving assembly line operation;
3. Intelligent control to achieve IoT connectivity of client MES systems.
Project case: Automotive components BMW CTV and other projects;
Applicable materials: zinc alloy, aluminum alloy, copper and other metal components;
Application time: Since 2018.
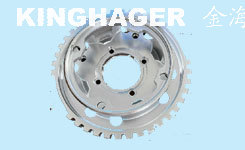
Before
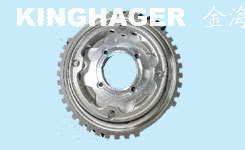
After

Automatic part taking/cooling/punching/ray system for die-casting island
The advantages of the die-casting island automatic pick-up/cooling/punching/ray system:
1. Swinging plate → robot loading (positioning plate) → robot picking/discharging (inside the processing equipment) → conveying;
2. Adopting precision multi-station turntable positioning fixtures, robotic arms in conjunction with processing equipment, with a high degree of automation;
3. No dust is generated during the process, reducing the workload of operators;
Intelligent control, voice operation step prompts, controllability of each link, selection of multiple material numbers, display of alarm positions, etc., achieving IoT connection of the client MES system;
Project cases: AUTOLIV, TAKATA safety buckle, SR SUNTOUR front fork and other projects;
Applicable materials: zinc alloy, aluminum alloy, copper and other metal components;
Application time: Since 2016.
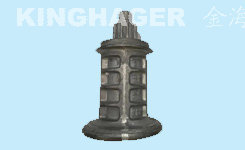
Before
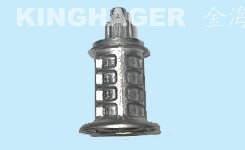
After